Paper is an analog variable in the world of digital printing. It directly affects the hue in the highlights, it affects the entire color gamut size for the print job, has a powerful impact on shadows, and is often outside the control of the production workflow.
While many people believe that traditional color management is about managing the CMYK inks and their separations, paper has as much of an influence on the color of the final printed piece as it does on the mechanical and chemical action of the inks or toners. Although a given paper brand’s attributes may be consistent, paper characteristics are not standardized. There is variation in attributes between mills as well as variation around an attribute property from a given mill. Paper is considered a commodity but its properties are a long way from standardized.
A lot has changed in the world of paper. One of the biggest changes in recent years has been the increased use of optical brightening agents (OBAs) in many papers to give the appearance of a very bright white paper. Printers have been known to accuse paper companies of using cheaper goods and “cheating” by using optical brighteners.
The initial choices made on paper selection might not take into consideration the impact later in the production chain, and sometimes those decisions can have unintended consequences.
White papers are not RGB 255,255,255. Paper companies control the shade of their papers by adding dyes and other chemicals to affect appearance. More dyes, less reflection, more color compensation. The paper owns some of the color space so detail that requires paper’s hue cannot be reproduced. The recent trends toward blue white papers have resulted in more and more dyes in the paper and further deviations from neutral. Some of today’s papers are equivalent to a 3 percent cyan screen.
Modern color management solutions do allow you to bias your results to either a strictly neutral result with no consideration of paper color, or to neutrality based on the paper color.
This can be very important, as the human eye will quickly key in on the “white” of the paper and judge other colors on the paper based on that shade.
Paper shade, or white point, is the key attribute of paper and is measured using L*a*b* based on CIE XYZ. Described by these three values, color management applications calculate complex color inter- pretations to characterize paper and predict paper’s effect on color reproduction.
OBAs are used to increase the apparent brightness and whiteness of papers and their use is becoming more prevalent in paper manufacturing. They increase brightness and whiteness by absorbing energy in the ultra violet and emitting (fluoresce) the energy in the blue area of the visible spectrum. Because, to the eye, blue/white looks "whiter" than yellow/white OBAs are not really whiteners, but bluing agents. OBAs are also used in ink to expand gamut or brighten 4/C image printed on poor substrates - e.g. newsprint.
While it is not practical for printers to quantitively measure the OBA content of the materials that they use, it is quite an easy matter to qualitatively see the OBA content. All it takes is an inexpensive (less than $15 USD) "black light."
For example, with the black light it is easy to see that the paper used for the Pantone Goe system swatch book (on the left in the image below) contains more OBAs than the conventional Pantone spot color swatchbook on the right. Also, it's clear that the uncoated paper section in the Pantone spot color swatchbook contains more OBAs than the coated section.
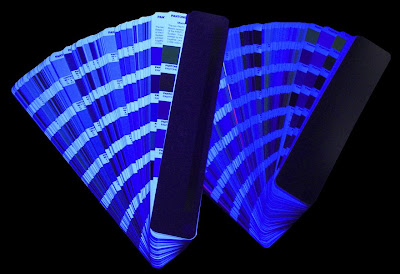
In reality, the rise in the use of brighteners can be attributed to a host of reasons, including production efficiency for maintaining a consistent look to a paper with changing content and a desire from customers for a brighter sheet at lower cost.
Another, more subtle problem can be the intended colorcast of the sheet. While in some ways we might consider OBAs an unintended colorcast, designers will sometimes purposefully choose a paper that has a colorcast.
The inks that are typically used in four color process printing block, to varying degrees, the fluorescence in papers containing OBAs. Black and magenta block the greatest amount, yellow a lesser amount, and cyan ink least of all. What this means is that when an image is printed using a halftone screen, lighter/pastel tones allow more more of the brightening and color shift of OBAs (towards blue) than the shadows. Color is effectively skewed towards the blue from shadows to highlights – but only when the paper being printed on has a high OBA content.
-----
Maintaining proper viewing conditions for print evaluations is a key part of color management.
The standards for viewing booths have changed over the past couple of years with the most recent release of ISO 3664 Graphic technology and photography — Viewing conditions.
If paper contains optical brighteners, color matching must be done in reference light conditions. When proofing on job stock that contains optical brighteners, it is important to critically examine both separations and curve effectiveness in the cyan containing highlight areas. The cyan/yellow color balance is hardest to achieve with these papers.
Even proofing papers contain optical brighteners. Creating profiles on these papers requires interpretation and tweaking if the press papers have a different level of optical brighteners or if the press papers have no optical brighteners.
Finally, optically brightened papers lose their fluorescence over time especially if exposed to light. The paper yellows. Print hues shift. Once printed, there is no recovery of the original paper whiteness so this should be kept in mind when a job reprints. Trying to match a first printing several months after completion is almost impossible. New proofs are a minimum requirement.
What additional tools can color management bring to the table to help tame the paper problem?
Traditionally, the way to “solve” OBA problems was to ignore them, primarily by using a filter that cut the UV light to stop it from hitting the paper and thus prevented the brightening effect of the OBAs. This is still a very effective approach to process control, but it is no longer the norm in color management. The other way we ignored it was by doing just that, not acknowledging the problem.
Today, we are much more likely to solve the OBA problem by quantifying the amount of OBA by including the UV in the measurement and then adjusting the ICC profile to compensate for its presence. Some recent color solutions provide Optical Brightener Correction (OBC) technology, which allows you to fine tune the profile results by evaluating specific test charts against a series of Munsell color standards in the target viewing condition. This combination of physical standards and measured results allows for a uniquely precise correction for optical brighteners.
An additional parameter that can be handled in color management is the final viewing environment. Traditionally, a graphic arts workflow targets a daylight illuminant (usually noted as D50/2 – describing the illumination and viewing angle). One additional way to fine-tune the result is to define the viewing condition of the final destination or illumination at the intended point of use if it is not D50.
This can be done by either using CIE defined illuminants or by actually measuring the lighting in the final environment.
-----
And what about Glossy Paper?
Paper gloss is related to surface roughness and therefore affects color reproduction. Light of all wavelengths is reflected from the surface of paper. How it is reflected defines both its gloss and dot gain characteristics.
If the paper is glossy and smooth, it scatters less light and there is less dot gain. Light is reflected almost like a mirror (specular reflection).

Papers from different manufacturers absorb ink and toner/developer solution differently. There is no overall standard for surface roughness, ink absorptivity or developer absorptivity within the paper classification scheme. For the most accurate color, press profiles should be made on the chosen stock for a particular job.
Matte and uncoated papers are even more variable.
The best color reproduction will occur on:
The best color reproduction will occur on:
- Bright papers with uniform spectral reflection;
- Papers that are smooth and glossy;
- Papers that are neutral in shade; and
- Papers that exhibit minimal fluorescence.
----------
Do you have a color management question, horror story or event to share?
Email me at reilley4color@gmail.com